改性氧化铝/有机硅弹性体复合材料的热导率和低介电常数显著提高
Dan Yang, Shuo Huang, Mengnan Ruan, Shuxin Li, Jinwei Yang, Yibo Wu, Wenli Guo, and Liqun Zhang
Inspired by unparalleled adhesion of mussels, bioinspired poly(dopamine) (PDA) has been used to functionalize the surface of aluminum oxide (Al2O3) nanoparticles aiming at improving the thermal conductivity of silicone rubber (SR). The successful and effective preparation of PDA modified Al2O3 nanoparticles (Al2O3–PDA) was confirmed by XPS, HR-TEM, and XRD. The PDA coating on the Al2O3 nanoparticles improved its interfacial interaction between polymeric matrix and facilitated the uniform-dispersion of filler, leading to the 30 vol % Al2O3–PDA/SR composite that exhibited a high thermal conductivity (0.585 W/((m·K))), which was almost 400% of pure silicone rubber (0.147 W/(m·K)). In addition, the 30 vol % Al2O3–PDA/SR composite displayed a relatively low dielectric constant (4.06 at 1 kHz), which was a bit higher than that of pure SR (2.59 at 1 kHz), a big advantage for the electronic or electrical engineering application. With advantages of efficient, easy handling, controllable, and eco-friendly, this modification method provides a new universal route to improve the thermal conductivity of composites.
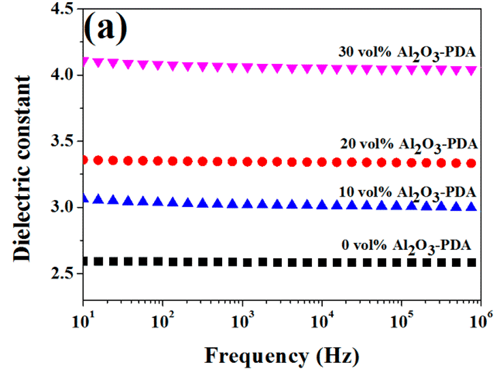
- Introduction
With increasing power densities in modern microelectronic devices, the growing demand for dissipation of generated heat has prompted great interest in dielectric materials. (1−3) Polymer composites consisting of a polymeric matrix and thermally conductive fillers are usually applied in preparing high thermal conductivity materials because of easy processability and low cost. Silicone rubber (SR) is a typical kind of engineering polymeric material to be used in cable accessories, gate dielectrics, and electronic devices, because it has excellent electrical insulation, relatively low dielectric constant, high elasticity, small mechanical hystersis, high breakdown strength, and easy film formation and can be used in a wide range of temperature. (4−6) However, the thermal conductivity of SR is relatively low, which limits its wider use as a thermally conductive material in industry.
During recent years, the most efficient strategy to improve the thermal conductivity of silicone rubber is to introduce a high thermal conductivity filler, such as carbon materials, (7) ceramic, (8) metal particles, (9) and metal oxide. (10) Though carbon materials have the advantage of high thermal conductivity and low weight, the increased cost and decreased electrical insulation of composites limit their wide applications, especially in electronic packaging needing a high electric breakdown field. Therefore, various low-cost inorganic ceramic fillers (Al2O3, (10,11) BN, (3,12) SiN, (5) SiC, (13) etc.) are used as the heat conductive fillers in wide application. However, the weak interfacial interaction between fillers and the matrix will result in inhomogeneous dispersion and agglomeration, which further lead to enhancement of interfacial thermal resistance. To improve the interfacial interaction, surface treatment and functionalization have been demonstrated to be efficient methods, (14) such as hydroxylation, (15) coupling agents, (16) surfactants, (17,18) and phosphoric acids. (19,20) Yang et al. (1) improved interfacial action between hexagonal boron nitride (h-BN) microparticles and a polyimide (PI) matrix by functionalizing h-BN with [3-(glycidyloxy)propyl]trimethoxysilane (g-MPS), during preparation of thermally conductive composites. Wang et al. (21) modified aluminum nitride (AlN) microspheres by (3-aminopropyl)triethoxysilane (KH550) and then added KH550 modified AlN into an ultrahigh molecular weight polyethylene (UHMWPE) matrix to prepare thermally conductive polymer composites. The results showed that the composites filled with modified AlN displayed much higher thermal conductivity than the commercial AlN/UHMWPE composites. Although these modification methods can improve the dispersion of particles to a certain extent, there still are some practical limitations, such as multistep production, complex instruments, and environmental unfriendliness. Especially, these chemical reactions need additional heating equipment, resulting in high energy cost.
Recently, marine mussel adhesive has attracted broad interest due to their marvelous properties. (22,23) It is believed that dopamine, containing 3,4-dihydroxy-l-phenylalanine (L-DOPA) and lysine amino acids (lysine), is the first molecule to display material-independent surface modification because the poly(dopamine) (PDA) film has the ability of attachment to various inorganic and organic substrates, owing to the strong hydrogen bonding from its abundant catechol groups. (23,24) In addition, the PDA provides secondary reactivity with various functional groups, including thiol, amine, and quinone itself via Michael addition or Schiff base reactions, serving as a versatile platform for secondary reactions with further specific functionalization. (25,26) Recently, PDA has been demonstrated in the literature to be a popular modifier to enhance the interfacial adhesion between an inorganic filler and a polymeric matrix. (27−30)
Here, we report an efficient and easy approach to improve the thermally conductivity of silicone elastomer using bioinspired PDA to modify aluminum oxide (Al2O3) nanoparticles. The Al2O3 nanoparticles were used in our work due to their high thermal conductivity (32 W/(m·K)), low cost, and stable chemical performance. (31) The successful deposition of PDA on the Al2O3 surface was demonstrated by XPS, HR-TEM, and XRD. The effects of the PDA layer on the thermal conductivity and dielectric properties of silicone elastomer composites were studied. Indeed, the cost of dopamine monomers is relatively high for extensive industry production. Fortunately, research shows that low cost catechol and polyamine could polymerize and deposit on the surface of substance with adhesive properties similar to those of PDA. (32,33) In our future, we will use low cost catechol and polyamine for the replacement of dopamine to improve the interfacial interaction between the inorganic nanoparticles and polymeric matrix.
- Experimental Section
2.1. Materials
Silicone rubber (110-2) was supplied by Chenguang Research Institute of Chemical Industry, Sichuan Province, China. The α-Al2O3 nanoparticles with type AKP-30 (with an average diameter of 300 nm) were provided by Sumitomo Chemical. The cross-linking agent of dicumyl peroxide (DCP) was provided by from the Beijing Chemical Plant. Dopamine hydrochloride (dopamine, 99%) and tris(hydroxymethyl)aminomethane (Tris, 99%) were received from Beijing Chemicals Co., Ltd.
2.2. Coating of PDA on Al2O3 Nanoparticles
First, 0.2 g of dopamine was immersed in 100 mL of distilled water to prepare the dopamine solution (2.0 g/L), followed by addition of Tris, which can form a Tris–HCl buffer solution, and its pH was adjusted to 8.5. Then, 15 g of Al2O3 nanoparticles was immersed into the above solution and under magnetic stirring for 24 h at 25 °C. Last, the modified Al2O3 nanoparticles were collected via filtration and washed three times with deionized water (denoted as Al2O3–PDA). The filter material is a commercial medium-speed qualitative filter paper with 100% cotton cellulose of type 102, which is supplied by Hangzhou Special Paper Industry Co., Ltd. Parts a and b of Figure 1 present the procedure for surface functionalization of Al2O3–PDA nanoparticles and the possible reaction mechanism of dopamine self-polymerization.
Figure 1
Figure 1. Illustration of (a) procedure for preparation of Al2O3–PDA nanoparticles, (b) possible mechanism of dopamine oxidative self-polymerization, and (c) hydrogen bonding formed in Al2O3–PDA/SR composites.
2.3. Preparation of SR Composites Filled with Al2O3 and Al2O3–PDA Nanoparticles
First, 80 g of silicone elastomer was put into a 6 in. double-roll open mill. Then, 0, 10, 20, and 30 vol % Al2O3 or Al2O3–PDA particles were mixed. Afterward, 2 g of DCP and 20 g of silicone oil mingled with the rubber matrix. The obtained uncured composites rested for 24 h to ensure good dispersion of ingredients. Last, the uncured composites were vulcanized at 160 °C and 25 MPa for T90 (optimum cure time). A curemeter (GT-M2000-FA Goteah Limted Co.) was used to determined the T90.
2.4. Characterization Methods
High resolution transmission electron microscope (HR-TEM) studies were conducted on a H 9000 (Hitachi) to observe surface morphologies of the Al2O3 and Al2O3–PDA nanoparticles.
X-ray photoelectron spectrometry (XPS) was recorded on an ESCALAB 250 spectrometer (Thermo Electron Corporation) with an Al Kα X-ray source (1486.6 eV) to determine chemical compositions of the samples.
Powder X-ray diffraction (XRD) patterns were taken on a D8 Focus X-ray diffractometer (Bruker) to investigate the crystalline structure of the Al2O3 and Al2O3–PDA nanoparticles.
Thermogracimetric analysis (TGA) was performed in the temperature range 30–540 °C with a heating rate of 20 °C/min by using a TA Q500 thermogravimetric analyzer. The TGA experiments were carried out under a nitrogen atmosphere.
Scanning electron microscopy (SEM) images of SR composites filled with Al2O3 and Al2O3–PDA nanoparticles were taken on a FEI NanoSEM 430 field-emission scanning electron microscopy. Prior to observation, a layer of gold was sputtered on the fractured surfaces of samples to avoid charge accumulation.
The elemental composition of the samples was observed by using a scanning electron microscopy (SEM, SSX-550) equipped with an energy dispersive X-ray spectroscopy (EDX) detector. Prior to observation, a layer of gold was sputtered onto the fractured surfaces of samples to avoid charge accumulation.
The dielectric properties were measured using a Novochtrol Alpha-A impedance analyzer over the frequency range 101–106 Hz at room temperature.
The volume resistivity of SR composites was measured using an EST 121 resistivity meter (Beijing Huajinghui Technology Co. Ltd., Beijing, China). The volume resistivity (ρv) of samples can be calculated according to following equation:
where L is the thickness of the specimen, Rν is the resistance of the specimen, and d is the diameter of the electrode.
The thermal conductivity of samples was measured using a HC-110 thermal conductivity meter (Laser Comp. Inc.). The temperatures of the hot and cold plates of the thermal conductivity meter were 20 and 40 °C, respectively. The pressure was 414 kPa.
- Results and Discussion
3.1. Coating of PDA on Al2O3 Nanoparticles
The surface chemical compositions of Al2O3 nanoparticles before and after PDA deposition were investigated by recording the XPS wide scan, N 1s core-level spectra, and C 1s core-level spectra, as shown in Figure 2. As we all know, the samples will contact with air inevitably during save, transport, and analyze; therefore, the C 1s signal in pristine Al2O3 particles mainly comes from the contaminant. (34) It can be noted that in Figure 2a,b, Al2O3 and Al2O3–PDA nanoparticles exhibit both peaks of C 1s and O 1s but a new peak component of N 1s species was only observed in Al2O3–PDA nanoparticles at a binding energy (BE) of about 400 eV. Figure 2d shows the N 1s core level spectrum of Al2O3–PDA nanoparticles was deconvoluted into two peaks at BEs of 398.5 and 399.5 eV, attributable to ═N– species and N—H species from dopamine and dopamine self-polymerization. The C 1s XPS spectra of pristine Al2O3 particles can be deconvoluted into two peak components at binding energies of about 284.6 and 286.4, attributed to the C—C and C—O species, respectively. However, two additional peaks of C—N and O—C═O species at 285.5 and 288.5 eV appear in Al2O3–PDA nanoparticles, which can be another fingerprint of PDA coating on Al2O3–PDA nanoparticles. In addition, determined by XPS spectra of pristine Al2O3 nanoparticles, the C, N, and O concentrations are 35.5%, 41.6%, and 0.76%, respectively. After PDA was coated on Al2O3 nanoparticles, the O/C ratio increases from 0.85 to 1.03, attributed to the higher O/C ratio of PDA than that of pristine Al2O3 nanoparticles. These above results demonstrate the successful self-polymerization of dopamine on the Al2O3 nanoparticles.
Figure 2
Figure 2. XPS wide-scan, N 1s core-level spectra, and C 1s core-level spectra of (a, c, e) Al2O3 and (b, d, f) Al2O3–PDA nanoparticles.
The surface topographies of Al2O3 nanoparticles before and after treatment by PDA were observed by HR-TEM. Figure 3a shows that the pristine Al2O3 nanoparticles display a smooth surface. By contrast, the surfaces of Al2O3–PDA nanoparticles exhibit a distinct and continuous deposition layer with a thickness of ≈2 nm (shown in Figure 3b), providing further evidence for deposition of PDA on Al2O3 nanoparticles. In addition, the PDA amount on the surface of Al2O3 particles is 1.89%, according to calculations by TGA and gravimetric methods (shown in Figure S1). Until now, the mechanism of dopamine self-polymerization is still under some debate. It is widely thought that the catechol groups first oxidized into quinone at weak alkaline PH, which then forms a key intermediate 5,6-dihydroxyindole (DHI) through rearrangement and intramolecular cyclization via 1,4-Michael addition. The DHI further oxidized into 5,6-indolequinone, which can further undergo intermolecular cross-linking to form a PDA layer, an amelanin-like polymer (shown in Figure 1b). (25,35−37)
Figure 3
Figure 3. HR-TEM images of (a) Al2O3 and (b) Al2O3–PDA nanoparticles.
The XRD diffraction patterns of the Al2O3 and Al2O3–PDA nanoparticles are presented in Figure 4. Comparing with XRD patterns of Al2O3 and Al2O3–PDA nanoparticles, we can see that the characteristic peaks of Al2O3 and Al2O3–PDA nanoparticles show the same diffraction peaks, suggesting that the coating process of PDA does not affect the crystal structure of Al2O3 nanoparticles and the thin PDA layer is amorphous.
Figure 4
Figure 4. XRD patterns of (a) Al2O3 and (b) Al2O3–PDA nanoparticles.
3.2. Microstructure of SR Composites Filled with Al2O3 and Al2O3–PDA Nanoparticles
To directly observe the filler dispersion in SR composites, we took SEMs to investigate, which are shown in Figure 5. To determine the elemental composition of white spots in the SEM images, the EDX spectrum of the white spots in 30 vol % Al2O3/SR composite was tested and shown in Figure 5e. From Figure 5e, we can find the elemental content ratio of Al to O is 2/3, demonstrating the particle is Al2O3. It can be seen that the Al2O3 nanoparticles are exposed on the fractured surfaces in Figure 5a, indicating a poor interfacial adhesion between the Al2O3 nanoparticles and SR matrix. When the content of Al2O3 nanoparticles increases to 30 vol %, there are some serious agglomerates in the SR composite. On the contrary, the Al2O3–PDA/SR composites exhibit better dispersion and smoother fractured surfaces than the Al2O3/SR composites. Especially in the SR composite filled with 10 vol % Al2O3–PDA nanoparticles, almost every individual Al2O3–PDA nanoparticle is surrounded by a layer of polymeric matrix, attributed to compatibility between the filler and matrix being improved by dopamine modification. In addition, FTIR measurements were used to analyze the interaction between Al2O3–PDA and the SR matrix, which is shown in Figure S2. The absorption peaks at 1085 cm–1, which are attributed to Si–O–Si symmetric stretch shifts to higher wavenumbers in the Al2O3–PDA/SR composites, is attributed to the formation of hydrogen bonding between the dopamine and SR. (38,39) The illustration of hydrogen bonding formed in Al2O3–PDA/SR composites is shown in Figure 1c. These results demonstrated that PDA can provide strong adhesion to the surface of Al2O3 nanoparticles and SR macromolecules.
Figure 5
Figure 5. SEM micrographs of SR composites filled with (a) 10 vol % Al2O3, (b) 10 vol % Al2O3–PDA, (c) 30 vol % Al2O3, and (d) 30 vol % Al2O3–PDA nanoparticles. (e) EDX spectrum of white spots in 30 vol % Al2O3/SR composite.
3.3. Mechanical Properties of SR Composites Filled with Al2O3 and Al2O3–PDA Nanoparticles
To evaluate the mechanical properties of SR composites filled with different volume fractions of Al2O3 and Al2O3–PDA nanoparticles, tensile tests were performed. The stress–strain curves are presented in Figure 6. By comparing with pure SR, an increase of tensile strength and elongation at break are easily observed by SR composites. The tensile strength of 30 vol % Al2O3/SR composite and 30 vol % Al2O3–PDA/SR composite are increased from 0.17 MPa for pure SR to 1.77 and 1.29 MPa, respectively. The much increased tensile strength can be explained by enhancement of inorganic fillers. In addition, comparing with Al2O3/SR composites, the Al2O3–PDA/SR composites display a lower tensile strength at the same content of filler. This phenomenon might be responsible due to two competing factors. One is the strong interfacial interaction between Al2O3–PDA nanoparticles and the SR matrix will improve filler dispersion and suppress the mobility of polymer chains, thus increasing the tensile strength. Second is the softening effect as a result of the rigid Al2O3 nanoparticle coated by a PDA layer having a much lower modulus than that of pristine Al2O3 nanoparticles. The PDA layer will increase the volume fraction of whole polymeric phase in SR composites. (30) Assuming that the Al2O3 nanoparticle was spherical and 171 g of Al2O3 nanoparticles was incorporated into 100 g of the SR matrix (with volume fraction of 30%), we can calculate the volume of the PDA layer (VPDA) coated on the Al2O3 nanoparticles roughly according to the following equation:
where r and VsAl2O3 are the radius and volume of signal Al2O3 nanoparticle, respectively, nAl2O3 is the number of Al2O3 nanoparticles in the matrix, mAl2O3 is the weight of all the Al2O3 nanoparticles in the matrix (i.e., 171 g), h is the thickness of the PDA (i.e., 2 nm), and ρAl2O3 is the density of Al2O3 nanoparticles (i.e., 4.0 g/cm3). It was found that the polymeric volume introduced by the PDA coating is about 1.71 cm3, whereas the volume of Al2O3 nanoparticles (VAl2O3) is about 42.75 cm3 in the ca.100 cm3 SR. The softening effect of Al2O3–PDA nanoparticles is the dominant factor, and the interfacial interaction has a small impact on tensile strength, leading to the tensile strength of Al2O3–PDA/SR composites being lower than that of Al2O3/SR composites. In addition, the elongation at break of the SR composite filled with 30 vol % Al2O3 or Al2O3–PDA nanoparticles is almost 3 times that of pure SR. This phenomenon can be explained by the decreased cross-link density of SR composites after filling with inorganic filler. The interference of inorganic nanoparticles on the cross-linking process of elastomer also can be found in associated literature. (30) Usually, a low cross-link density will lead to a large elongation at break. Moreover, comparing with Al2O3/SR composites, Al2O3–PDA/SR composites display a larger elongation at break at the same content of filler, ascribed to strong interfacial interaction and uniform dispersion with fewer defects.
Figure 6
Figure 6. Stress–strain curves of SR composites filled with different contents of Al2O3 and Al2O3–PDA nanoparticles.
3.4. Thermal Properties and Dielectric Properties of SR Composites
Figure 7 shows the in-plane thermal conductivity of Al2O3/SR composites and Al2O3–PDA/SR composites. The results demonstrate that thermal conductivity of SR composites increases with the fraction of Al2O3 nanoparticles whether they are modified by PDA or not. This can be explained by compact thermally conductive chains or pathways that can be easily formed in polymeric composites with the increase of the volume fraction of fillers. In addition, the higher thermal conductivity fillers introduced into the SR matrix will cause the thermal conductivity of the SR composites to increase. Meanwhile, we can find the thermal conductivity difference between Al2O3/SR composites and Al2O3–PDA/SR composites is not considerable at low content. With increasing filler content, the increase of Al2O3–PDA/SR composites is faster than that of Al2O3/SR composites. It may be due to the fact that the thermally conductive particles surrounded by the SR matrix cannot touch each other at the low loading. As the volume fraction of the filler increases, the Al2O3–PDA/SR composites display better dispersion and the thermally conductive chains can be formed more easily in comparison with Al2O3/SR composites. The schematic diagram of dispersion of Al2O3 and Al2O3–PDA nanoparticles in SR composites is shown in Figure 8. Therefore, the largest thermal conductivity of 0.585 W/(m·K) is obtained by SR composite filled with 30 vol % Al2O3–PDA, which is almost 400% of SR without filler.
Figure 7
Figure 7. Thermal conductivity and dielectric constant (1 kHz) of SR composites filled with different contents of Al2O3 and Al2O3–PDA nanoparticles.
Figure 8
Figure 8. Schematic diagram of dispersion of Al2O3 and Al2O3–PDA nanoparticles in the SR matix.
The room temperature dielectric properties of samples were investigated by dielectric relaxation spectroscopy. Figure 7 displays dielectric constant of pure SR and SR composites at frequency of 1 kHz. From Figure 7, we can find the dielectric constant of all composites increase with increasing volume fraction of filler. There are two reasons can be explained for this result. First, the dielectric constant of Al2O3 nanoparticles is higher than that of SR matrix. Second, an increase in dipole polarization of Al2O3 particles and interface polarization between the SR matrix and Al2O3–PDA particle. (5) In addition, the dielectric constant of Al2O3–PDA/SR composites is higher than that of Al2O3/SR composites at the same filler content, ascribed to the uniform dispersion of Al2O3–PDA particles in the SR matrix. (16) Poor dispersion and poor interfacial adhesion between the nanoparticles and the polymeric matrix is a key factor for low dielectric constant. (40) However, the 30 vol % Al2O3–PDA/SR composite displayed a relatively low dielectric constant (4.06 at 1 kHz), which is a bit higher than that of pure SR (2.59 at 1 kHz), a big advantage for the electronic or electrical engineering application. The frequency dependence of dielectric properties of SR composites filled with different volume fraction of Al2O3–PDA nanoparticles is shown in Figure 9. From Figure 9a, we can observe the spectra of dielectric constant of all samples are almost flat over the entire range of frequency, indicating the polarization in composites can catch up with the frequency change of electric field. (41) On the contrary, the dielectric loss tangent exhibits a dramatically decrease at the low frequency range of 101–103 Hz, as shown in Figure 9b. However, the dielectric loss of the composites is also increased with increasing volume fraction of Al2O3–PDA particles. For example, the dielectric loss tangent of the 30 vol % Al2O3–PDA/SR composite at 100 Hz is increased from 0.001 for pure SR to 0.004. In short, the dielectric loss tangent of all composites is lower than 0.01 over the wide frequency range, a big advantage for dielectric materials in a wide application.
Figure 9
Figure 9. Dependence of (a) dielectric constant and (b) dielectric loss tangent of SR composites on frequency at different contents of Al2O3–PDA nanoparticles.
3.5. Volume Resistivity of SR Composites
To investigate the insulating property of Al2O3/SR composites and Al2O3–PDA/SR composites, the volume resistivity was measured. As shown in Figure 10, the volume resistivity of SR composites decreases with the increasing volume fraction of Al2O3 or Al2O3–PDA nanoparticles, ascribed to the higher electrical conductivity of Al2O3 nanoparticles than that of the SR matrix. However, the volume resistivities of Al2O3–PDA/SR composites are a little higher than those of Al2O3/SR composites at the same filler content. This pehemenon can be explained by the insulating PDA hindering the electron transition of the composites, thus improving the volume resistivity. (16,42) However, the volume resistivity of all of samples is higher than 1 × 1013, indicating the composites are insulated and can be used in electrical insulation field.
Figure 10
Figure 10. Volume resistivity of SR composites filled with different contents of Al2O3 and Al2O3–PDA nanoparticles.
- Conclusion
The Al2O3 nanoparticles were successfully coated with an organic PDA layer through the biomimetic method. The organic PDA layer coating on the surface of Al2O3 nanoparticles improved the homogeneous dispersion of Al2O3–PDA/SR composites and increased the interfacial interaction between the inorganic nanoparticles and polymeric matrix. Therefore, the 30 vol % Al2O3–PDA/SR composite exhibited a high thermal conductivity (0.585 W/(m·K)), which was almost 400% of that for pure silicone rubber (0.147 W/(m·K)). However, the dielectric constant of 30 vol % Al2O3–PDA/SR composite is relatively low (4.06 at 1 kHz), which was a bit higher than that of pure SR (2.59 at 1 kHz), a big advantage for the electronic or electrical engineering application of SR composite. This biomimetic method is efficient, easily handled, controllable, and eco-friendly and can be used to modify other thermally conductive filler to improve thermal conductivity of composites.