电池用β″-氧化铝固体电解质的烧结行为
A. Niyompan, K. Srisurat, R. Tipakonthitikul, K. Pengpat and T. Tunkasiri
采用液相烧结法制备了适用于电动汽车电池系统的β″-氧化铝固体电解质。研究的主要目的是降低烧结温度,通常要求高达1700C。制备了x = 0.125的Na1-xMg2xAl5-xO8为mgo稳定的Naβ″-氧化铝。采用湿法球磨法制备了Na2CO3、MgO和γ -Al2O3的混合物。然后,在1200C下煅烧10小时。然后,在用干压技术成形之前,以不同浓度加入烧结助剂CuO。在不同温度下烧结绿色微球,固定停留时间4小时。煅烧粉末的相鉴定表明,β″-氧化铝以主要相的形式存在,β ' -氧化铝的比例很小。这两个相的共存在这个特殊的系统中是很常见的。添加CuO的烧结样品的相检验结果表明,烧结样品没有发生相变,但随着烧结温度和CuO含量的增加,β′-氧化铝的浓度比增大。在1550C烧结时,CuO含量较高(5和10 mol%)的陶瓷致密化程度较高。扫描电镜可以清楚地看到β″-氧化铝的层状结构。SEM结果还表明,CuO含量越高,晶粒发育越快,孔隙率越低。添加CuO的样品的直流电导率相对于未添加CuO的样品有合理的高。研究结果表明,采用液相烧结法制备的β″-氧化铝非常适合应用于电动汽车电池中。
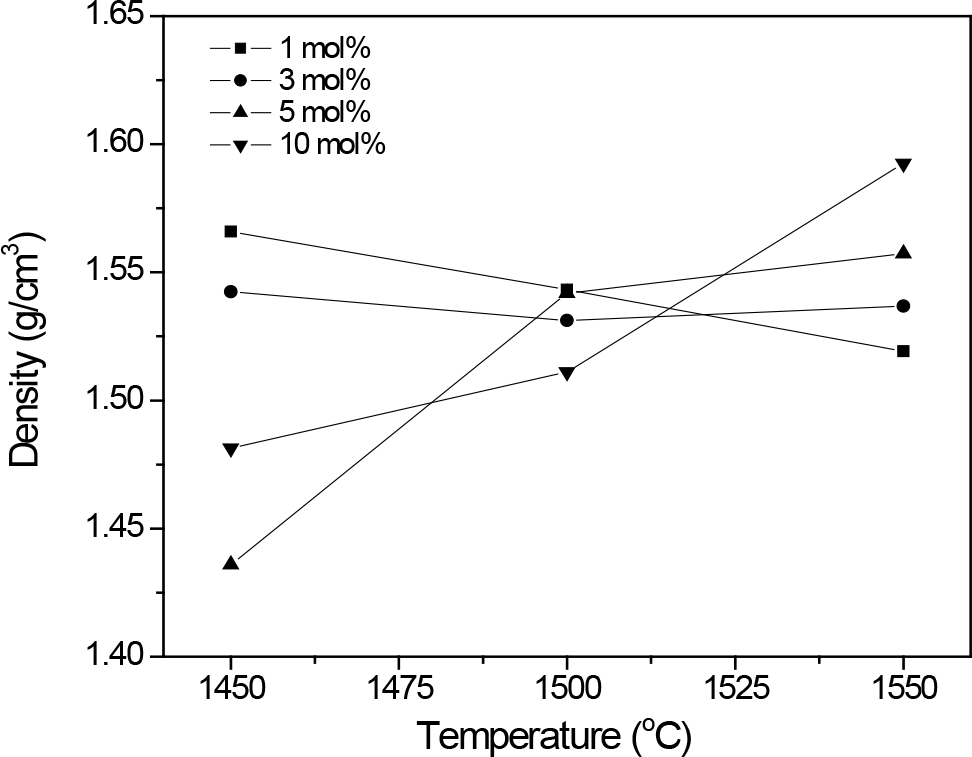
简介
采用β″-氧化铝固体电解质作为电动汽车电池的导电层已经实现,该产品的商业名称为ZEBRA电池[1,2]。通常,β″-氧化铝的标称成分为Na(1-x)Al5O8(其中0<x<3)[3],但需要加入MgO才能稳定β″-氧化铝。因此,相应的组合物变成Na1-xMg2xAl5-xO8,其中x基本上固定在0.175。然而,通过常规固相烧结制备的致密mgo稳定β″-氧化铝只能在较高的烧结温度(1700°C)下制备。在这种高烧结水平下,由于其挥发性,也可能发生钠含量的损失,导致成分的改变或有时涉及相变。这种高温烧结也不经济,需要特殊的仪器。为了克服这一问题,人们还采用了溶胶-凝胶法[4]和微波烧结等替代方法[5-7]。但这些方法工艺复杂,原料复杂,产量小。
本工作尝试采用液相烧结技术,寻找合适的降低镁稳定β″-氧化铝陶瓷烧结温度的制备路线。在此基础上,研究了添加剂存在下mgo稳定β″-氧化铝的烧结行为。选用CuO作为烧结助剂。从致密化和组织排列两方面研究了CuO的加入对合金组织的影响。还测定了对离子电导率的影响。
实验
根据β″-氧化铝的制备,采用高纯化学试剂Na2CO3、MgO和合成γ-Al2O3作为起始原料。本实验室用沉淀法煅烧制备的AlO(OH)得到γ-Al2O3。将γ-Al2O3、Na2CO3和MgO混合在YZT球介质中,根据所需的重量和球磨20小时,然后在1200℃下,加热速率和冷却速率为5℃/min,煅烧10小时。对煅烧后的粉末进行XRD相鉴定。在干压法制备绿色陶瓷球团之前,将不同比例的CuO加入到煅烧粉末中,分别为1、3、5和10 mol%。然后在1450-1550°C的温度范围内烧结4h,再次进行相鉴定。采用扫描电镜(SEM)对β″-氧化铝粉末和β″-氧化铝陶瓷的形貌进行了分析。采用室温空气和蒸馏水称重的阿基米德原理测定了烧结球团的密度。最后,用LCR仪测定了陶瓷样品的直流离子电导率。
结果与讨论
如图1所示为煅烧粉末的XRD谱图,其中β″-氧化铝为主要产物。β′-氧化铝的形态也可见,但所占比例很小。这两相共存似乎是这个特殊体系的共同产物,因为它们的氧堆叠序列[8]略有不同。
图1. 煅烧后的β″-氧化铝粉末的XRD图谱。
图2. 1450℃烧结β″-氧化铝陶瓷的XRD粉末形貌随Cu含量的变化。
不同cu含量和三种不同烧结温度下烧结样品的XRD粉末谱图如图2-4所示。在图2中,体陶瓷的相类型发生了变化,仍然观察到β″-Al2O3的存在以及杂质β ‘ -Al2O3。cu浓度的增加并没有引起两相相对强度的变化。当烧结温度升高到1500℃时,相关系变化也不明显,图2和图3中粉末形态的轮廓比较相似。然而,当烧结温度上升到1550℃时,含有较高CuContent的β″-Al2O3陶瓷的衍射峰开始出现(图4),同时也可以观察到β ‘ -Al2O3峰的相对强度变化。这些结果表明,较高的烧结温度和较高的cu含量会发生相变。部分β″-Al2O3可能转变为β′-Al2O3,部分分解生成α -Al2O3。这一观察结果并不令人惊讶,因为正如Näfe等人[9]所建议的那样,β″-β′转变在高温下容易发生。在此温度下烧结的样品中钠含量也有明显的损失,从而引起化学成分的改变和相变。α -Al2O3相的出现可能与CuContent的参与有关,当CuO含量为5和10 mol%时,其衍射峰明显。
图3. β″-氧化铝陶瓷在1500℃烧结时Cu含量变化的XRD粉末形貌。
图4. β″-氧化铝陶瓷在1550℃烧结时Cu含量变化的XRD粉末形貌。
图5. 研究了在不同温度和Cu浓度下烧结β″-Al2O3陶瓷样品的表观密度。
表1. 在300℃下测定了不同烧结温度下β″-Al2O3陶瓷的离子电导率(σ dc)。
烧结样品的表观密度测量值如图5所示,表明CuO对β″-Al2O3陶瓷烧结性能的影响仅在含有较高CuO(5和10 mol%)的陶瓷中观察到,随着烧结温度的升高,密度增加。在较低cu浓度下,CuO对β″-Al2O3致密化没有明显影响。
图6为1450℃烧结β″-Al2O3陶瓷的SEM形貌图。β″- Al2O3颗粒是多个血小板的填料。平板厚度和尺寸用CuContent显影。增加cu浓度也可以改善致密化,因为观察到的孔隙率更少。然而,这些样品的密度值并没有显示出与观察到的微观结构相同的趋势。这可能是由于β″-Al2O3血小板团簇的形成或CuContent分布不均匀的影响,从而影响了整体堆积密度。
表1报告了在300℃下测量的离子电导率。基本上,在压痕烧结温度下,样品应具有较高的离子电导率,但对于cu含量相同的每组样品,这似乎并不一定。但在相同的烧结温度下,CuConcentration对离子电导率的影响明显,CuConcentration越高,离子电导率越低。这并不奇怪,因为CuO杂质对Na+的迁移起到了阻碍作用。本文发现离子电导率的波动主要是微观结构排列的结果。密度值也反映了同样的效应。
图6. Cu含量:(a) 1 mol% (b) 3 mol% (c) 5 mol% (d) 10 mol% 1450℃烧结β″-Al2O3陶瓷的SEM显微形貌。
总结
添加助烧结剂CuO可提高β″-Al2O3陶瓷在1450 ~ 1550℃温度范围内的烧结性能。CuO含量高,烧结温度高,也会引起相变。这种变化也被认为是由于Na+的损失。在300℃下测定的直流离子电导率表明,陶瓷的微观结构和密度对Na+迁移率有很大的影响。