钠离子电池正极Na2Fe2(SO4)3@氧化铝复合材料及其制备方法
张治安, 陈晓彬, 宋俊肖, 李军明, 杨智伟, 李劼, 赖延清, 王飞, 任冠行, 宋润峰
The invention discloses a kind of nucleocapsid Na2Fe2(SO4)3@alumina composite materials and its preparation method and application, the material are by Na2Fe2(SO4)3The composite material of core-shell structure that particle surface coated aluminum oxide is formed.The present invention by organic aluminium salt pyrolysis cladding Na2Fe2(SO4)3, overcome Na2Fe2(SO4)3Shipwreck is dissolved in carry out the problem of alumina-coated by conventional hydrolysis method, and synthetic method is simple, mild condition, yield is high, the composite material being prepared can effectively inhibit " the surface poisoning effect " of material, with height ratio capacity, high working voltage, good stable circulation performance and excellent high rate performance during using as sodium-ion battery positive material.
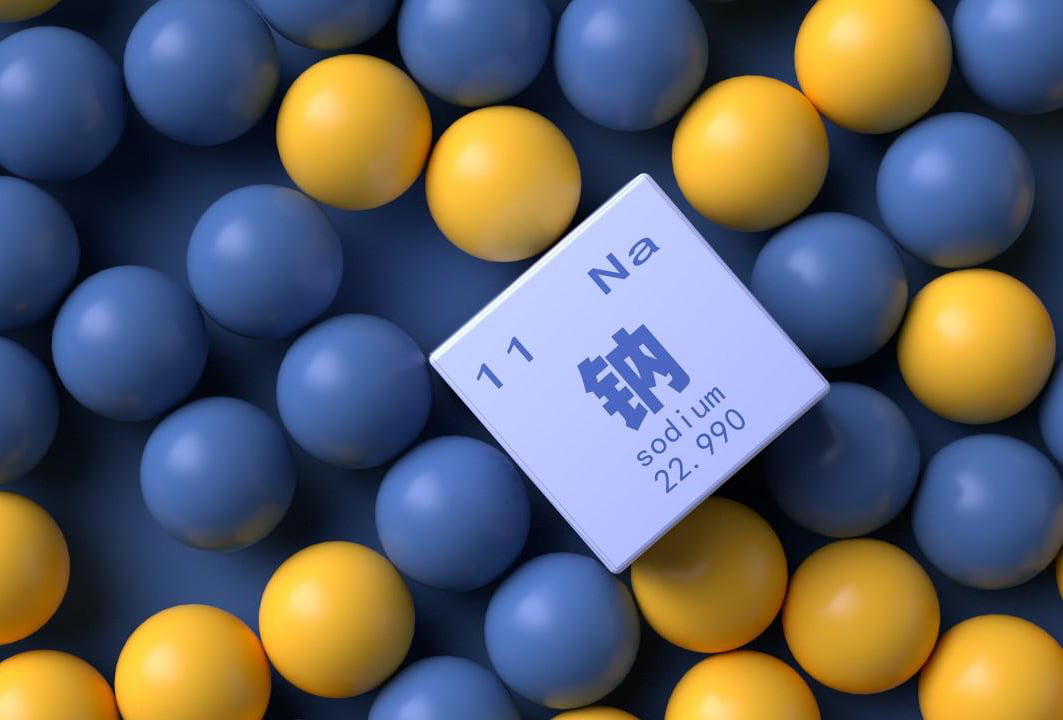
Technical field
The invention belongs to sodium-ion battery fields;More particularly to a kind of sodium-ion battery anode Na2Fe2(SO4)3@aluminium oxide Composite material and preparation method thereof.
Background technology
As lithium ion battery has achieved fast development in 3C Product and electric automobiles, and show good hair While exhibition prospect, since metal lithium resource is in the scarcity of crustal abundance, lithium ion battery is difficult to meet in large-scale energy storage field In large-scale application, manufacture cost also will be in the trend that constantly rises with the scarcity of lithium resource.Furthermore lithium ion battery by Bad in security, the development in electric vehicle and large-scale energy storage field is greatly limited.However, with elemental lithium phase Than, sodium element in the earth’s crust rich reserves and source is more extensive, and sodium element is in same master with lithium in the periodic table of elements Race, so having similar physicochemical property to lithium.Therefore, the manufacture cost of relative moderate and the sodium to compare favourably with lithium ion battery Ion battery becomes a kind of usable battery system of storage on a large scale of most potential achievable industry.However, due to sodium ion Ionic radius it is bigger than the ionic radius of lithium ion so that it is embedded with abjection ratio in electrode material in kinetically sodium ion Lithium ion is more difficult, and oxidation-reduction potential of the sodium ion with respect to calibration and larger atomic mass so that sodium-ion battery The low voltage of positive electrode, energy density be not high.Therefore, improve sodium-ion battery positive material voltage and energy density into For the emphasis of research.
Researchers have studied the sodium-ion battery positive material of different systems, wherein it is more representational be P2 types and O3 type layered oxide systems, such as P2-Na2/3[Fe1/2Mn1/2]O2, O3-NaFe0.5Co0.5O2, but the cycle life of these materials Short, voltage platform is relatively low.The shortcomings such as phosphate and pyrophosphate system and generally existing voltage platform are low.Na2Fe2(SO4)3Tool There are the theoretical plates of 3.8V, with the platform to compare favourably with lithium ion battery but since sulfate system easily draws with hygroscopicity Material surface poisoning effect is played, results in the problems such as material preparation process is harsh to production environment requirement, material property is unstable. Traditional alumina-coated achievees the purpose that alumina-coated, but Na by aluminium salt hydrolysis in aqueous solution2Fe2(SO4)3It is soluble in Water is difficult to realize the uniform cladding of aluminium oxide by the method.Technique for atomic layer deposition (ALD) due to expensive synthesis expense, And it relatively low yield, is difficult to realize the defects of large-scale production and is also difficult to meet Na2Fe2(SO4)3The needs of industrialized production.
The content of the invention
It is an object of the invention to provide a kind of Nano grade Na of the surface-coated aluminum oxide of nucleocapsid2Fe2(SO4)3 Composite material, the material are stablized with property, easily preserve, height ratio capacity, high working voltage, good stable circulation performance.
Another object of the present invention is to provide a kind of Na that coated with uniform aluminium oxide is realized using organic aluminium salt2Fe2 (SO4)3The preparation method of composite material;Be intended to provide a kind of mild condition, it is easy to operate, of low cost, can realize it is extensive The method of preparation.
A kind of sodium-ion battery anode Na2Fe2(SO4)3@alumina composite materials, by kernel and the shell of the cladding kernel Body forms;Wherein, the material for forming the kernel is Na2Fe2(SO4)3;The material for forming the housing is aluminium oxide.
The Na2Fe2(SO4)3@alumina composite materials crystal form is sodium fosfosiderite type;Grain diameter is 70~500nm.
Preferably, the Na2Fe2(SO4)3Kernel a diameter of 50~400nm;The thickness of the housing of cladding is 20 ~100nm.
The sodium-ion battery anode Na is prepared present invention additionally comprises a kind of2Fe2(SO4)3@alumina composite materials Preparation method comprises the following steps:
Step (1):Sodium source, sulphur source, source of iron are dissolved in water to obtain mixed solution;
Step (2):The mixed solution is evaporated into precipitation at 80~120 DEG C and obtains Na2Fe2(SO4)3Presoma;
Step (3):Presoma obtained by step (2) is sintered to obtain Na at 350~450 DEG C2Fe2(SO4)3Material;
Step (4):By the Na obtained by step (3)2Fe2(SO4)3Material is mixed with organic silicon source, then again 100~450 It is sintered at DEG C;Obtain the Na2Fe2(SO4)3@alumina composite materials.
The inventors discovered that helping to reduce dephasign using precipitation is evaporated at the temperature of this preparation method, shape is adjusted Looks;In addition the organo-aluminium heat decomposition cladding means of matching step (4) and the sintering temperature respectively walked again, effectively avoid surface poisoning from imitating Should, improve performance of the composite material of preparation in terms of electricity, such as chemically and thermally stability, cycle performance etc.;In addition, this hair Bright method mild condition, it is easy to operate, of low cost, can realize extensive preparation.
Na2Fe2(SO4)3It is difficult to carry out alumina-coated using existing Hydrolyze method;However, using other method for coating examples Such as technique for atomic layer deposition (ALD) somewhat expensive, production efficiency, low yield, it is difficult to realize mass produce.The present invention is innovatively By organic aluminium salt pyrolysis way come to Na made from step (3)2Fe2(SO4)3Material carries out in-stiu coating, composite wood obtained Material can effectively inhibit ” the surface poisoning effect ” of material, using as sodium-ion battery positive material when have height ratio capacity, High working voltage, good stable circulation performance and excellent high rate performance.
The sodium source is the water soluble salt using sodium as cation;The source of iron is the water solubility using iron as cation Salt;The sulphur source is the water soluble salt using sulfate radical or bisulfate ion as anion.
In the present invention, the sulphur source is not really wanted individually to add, it is possible to be provided by source of iron and/or sodium source.
The sodium source can be carbonate, bicarbonate, sulfate, disulfate, nitrate, acetate, the oxalic acid of sodium Salt, citrate etc..The source of iron can be water soluble trivalent iron salt or divalent ferrous salt, may be, for example, chlorate, nitre Hydrochlorate etc..The sulphur source can be using sulfate radical or bisulfate ion as ammonium salt, sodium salt, molysite of anion etc..
The molar ratio of sodium source, source of iron and sulphur source is to prepare Na2Fe2(SO4)3Subject to product;It that is to say, the sodium member of sodium source The molar ratio of the element sulphur (sulfate radical) of element, the ferro element of source of iron and sulphur source is 2: 2: 3.
Preferably, the sodium source is sodium carbonate, sodium acid carbonate, sodium acetate, sodium oxalate, sodium nitrate, sodium sulphate, sulfuric acid At least one of hydrogen sodium;The source of iron is frerrous chloride, ferrous sulfate, ferric nitrate, iron chloride, in ferric citrate at least It is a kind of;The sulphur source is at least one of sodium sulphate, niter cake, ammonium hydrogen sulfate, ammonium sulfate, ferric sulfate, ferrous sulfate.
In step (1), in the solution being configured to, the solubility of solute does not require, and appropriate concentration ratio is conducive to improve The treatment effeciency of subsequent step (such as evaporating precipitation).
Preferably, in step (1), in the solution being configured to, the molar concentration of the sodium ion of sodium source is 0.5-5mol/L; Further preferably 1-1.5mol/L.
The present invention prepares the Na by the way of evaporation, sintering2Fe2(SO4)3;It is grasped compared to existing preparation method Make simple;Material property obtained is good, is conducive to the in-stiu coating of subsequent alundum (Al2O3).
The inventors discovered that evaporating temperature has a certain impact to the performance tool of the material of preparation;At a temperature of described The generation of dephasign can be effectively reduced, is conducive to the speed for controlling crystal nucleation and growing up, adjusts the advantageous effects such as pattern.
The present inventors have additionally discovered that in step (1), the temperature of evaporation is more highly preferred to 80~100 DEG C;Preferred 80 DEG C.
The sintering process of step (3) carries out under oxygen-free atmosphere.
The oxygen-free atmosphere is protective gas or the protective gas doped with hydrogen.
Preferably, the sintering process of step (3) carries out under argon gas, nitrogen or hydrogen-argon-mixed atmosphere.
Hydrogen-argon-mixed atmosphere is the mixed gas of hydrogen and argon gas;Wherein, hydrogen volume is than being, for example, 5%.
The sintering temperature of step (3) is preferably 350 DEG C.
Preferably, the sintering process heating rate of step (3) is 2-8 DEG C/min;Further preferably 5 DEG C/min.
Sintering time is, for example, 20~30h;Preferably for 24 hours.
After the completion of the sintering processes of step (3), by Na obtained2Fe2(SO4)3Material and organic silicon source are uniformly mixed;It is mixed The mode of conjunction can be the prior art, such as grinding, ball milling etc.;Preferably ball milling, the ball milling are, for example, high-energy ball milling.
Preferably, organic silicon source is selected from least one of organic acid aluminium salt, aluminium alcoholates.
It the inventors discovered that at said temperatures can be equably on the inner nuclear material using organic silicon source Face forms alumina-coated layer.
The organic acid aluminium salt can be oxalic acid aluminium, aluminium citrate, C1~6 the organic acids such as carboxylic acid aluminium salt;Described Aluminium alcoholates can be existing common aluminium alcoholates, such as aluminium isopropoxide.
Preferably, organic silicon source in aluminium acetate, aluminium triformate, oxalic acid aluminium, propionic acid aluminium, aluminium isopropoxide extremely Few one kind.
More preferably, organic silicon source is selected from aluminium isopropoxide.
In step (4), the quality of organic silicon source, Na2Fe2(SO4)3The ratio of quality of materials is 1%~5%.
The inventors discovered that controlling the weight ratio, the Na with suitable cladding thickness can be obtained2Fe2(SO4)3@ Alumina composite material further improves the electric conductivity and other electric properties of obtained composite material.
Preferably, the quality of organic silicon source, Na2Fe2(SO4)3The ratio of quality of materials is 1.5%~2%.
Preferably, organic silicon source is aluminium isopropoxide, wherein, the quality of aluminium isopropoxide accounts for Na2Fe2(SO4)3Material Expect the 1.5%~2% of quality.
In step (4), organic silicon source and Na2Fe2(SO4)3It is sintered again under oxygen-free atmosphere after material mixing.
In step (4), the oxygen-free atmosphere is identical with the selection range of the sintering atmosphere of step (3);It is similarly protection Property gas or the protective gas doped with hydrogen.The protective gas is similarly nitrogen or inert gas.
Preferably, the sintering process of step (4) carries out under argon gas, nitrogen or hydrogen-argon-mixed atmosphere.
The hydrogen volume of hydrogen-argon-mixed atmosphere is than being, for example, 5%.
Preferably, step (4) and step (3) are sintered under identical atmosphere.
The sintering temperature of step (4) is more preferably 250~350 DEG C;It is more highly preferred to 250 DEG C.
The sintering time of step (4) is 2~10h;Preferably 4h.
By the preparation method, can be made with Na2Fe2(SO4)3For kernel, and in the core surface in-stiu coating oxygen Change the Core-shell structure material of the housing of aluminium;Wherein, the grain diameter of the core-shell material is 70~500nm;Wherein, the Na2Fe2 (SO4)3A diameter of 50~400nm of core (kernel), the thickness of alumina-coated layer (shell) is 20~100nm.
In the present invention, a kind of preferred Na2Fe2(SO4)3The preparation method of@alumina composite materials, comprises the following steps:
Step (a):It is 2: 2: 3 according to the molar ratio of sodium element, ferro element and element sulphur, source of iron, sulphur source, sodium source is distinguished It is dissolved in deionized water, stirs evenly, obtain mixed solution;
The sodium source is sodium carbonate, in sodium acid carbonate, sodium acetate, sodium oxalate, sodium nitrate, sodium sulphate, niter cake It is at least one;The source of iron is at least one of frerrous chloride, ferrous sulfate, ferric nitrate, iron chloride, ferric citrate;Institute Sulphur source is stated as at least one of sodium sulphate, niter cake, ammonium hydrogen sulfate, ammonium sulfate, ferric sulfate, ferrous sulfate;
Step (b):Gained mixed solution is placed in oil bath pan and is heated with stirring to 80~100 DEG C, solvent evaporated obtains Na2Fe2 (SO4)3Precursor powder;
Step (c):By precursor powder obtained by step (b) in 350~450 DEG C of sintering for 24 hours to get Na2Fe2(SO4)3Material Material;The atmosphere of sintering process is argon gas, nitrogen or hydrogen-argon-mixed (5%H2+ 95%Ar);
Step (d):By the Na obtained by step (c)2Fe2(SO4)3Material and organic aluminium salt grinding are uniform, and 2 are sintered at 250 DEG C ~10h;Sintering atmosphere is argon gas, nitrogen or hydrogen-argon-mixed (5%H2+ 95%Ar);
Organic silicon source is at least one of aluminium triformate, oxalic acid aluminium, propionic acid aluminium, aluminium isopropoxide.
The present invention further comprises the Na2Fe2(SO4)3@alumina composite materials are applied as sodium-ion battery just Pole material.
In application of the present invention, Na provided by the present invention is utilized2Fe2(SO4)3The application of@alumina composite materials is made It uses prior approach to be assembled into sodium-ion battery for sodium-ion battery positive material;And test its performance.
Na prepared by the present invention2Fe2(SO4)3The sodium-ion battery performance test methods of@alumina composite materials:It such as can For:Weigh above-mentioned Na2Fe2(SO4)3@alumina composite materials add in 10wt.% conductive carbon blacks as conductive agent, 10wt.% PVDF is as binding agent, and ground fully adding in a small amount of NMP is mixed to form uniform black paste slurry afterwards, by these slurries Coated in, as test electrode, with metallic sodium piece, electrode assembling becomes button cell as a comparison, uses in aluminum foil current collector Electrolyte system is 1M NaClO4/EC:DMC(1∶1).Charging and discharging currents density used in test loop performance is 120mAh g-1 (1C multiplying powers).
The method that the present invention is evaporated using solution has obtained Na2Fe2(SO4)3Presoma, and will further be obtained after sintering Na2Fe(SO)4Nucleocapsid Na is synthesized by simple solid-phase ball milling method2Fe2(SO4)3@alumina composite materials, gains Material is less with dephasign, and synthesis technology is simple, and covered effect is good.
Compared with prior art, it is an advantage of the invention that:
(1) cheap sodium source, source of iron, sulphur source is used to reduce cost as raw material.
(2) not only avoid and prematurely precipitate, reduce dephasign by strictly controlling solution evaporating temperature in the present invention Generation, reached control crystal nucleation and the speed grown up, adjusted the advantageous effect of pattern.
(3) dephasign is few in the presoma that the present invention is prepared, and activity is high, compared with the conventional method, can be in lower temperature It is evaporated by simple solution down, sintering obtains the Na of pure phase2Fe2(SO4)3@alumina composite materials.
(4) Na that the present invention obtains2Fe2(SO4)3@alumina composite materials, compared with the conventional method, which is in Existing nucleocapsid, alumina-coated is uniform, and cladding thickness is moderate, and cladding means are simple.
(5) present invention realizes Na using simple ball-milling method2Fe2(SO4)3Aluminium oxide uniformly coat, overcome tradition Na is caused using aqueous solution during Hydrolyze method coated aluminum oxide2Fe2(SO4)3The problem of dissolving, it is proposed that first use organic aluminium salt Coat Na2Fe2(SO4)3, then it is decomposed thermally to form by organic aluminium salt the new approaches of alumina-coated.
(6) the present invention overcomes the Na that existing method is prepared2Fe2(SO4)3/ C composite voltage platform is unstable, With serious hygroscopicity, the moisture-sensitive degree of production environment is reduced in the actual production process, effectively alleviates material ” table It is poisoned in face “, thermal stability is poor, easily decomposes the defects of generating sulfur dioxide.The present invention is the further optimization to scheme before, Hydro-thermal method prepares Na2Fe2(SO4)3High temperature high voltage resistant equipment is needed, preparation process is complicated, and poor repeatability is difficult to realize extensive life The shortcomings of production, the Na that the present invention is obtained by simple solvent evaporated method2Fe2(SO4)3@alumina composite materials have high electricity Pressure, voltage platform are stablized, and cycle performance is good, and chemical stability and thermal stability are more preferable, preparation process energy conservation and environmental protection, easy industry The advantages that change.
Description of the drawings
【Fig. 1】It is Na prepared by embodiment 12Fe2(SO4)3The X-ray diffractogram of@alumina composite materials;
【Fig. 2】It is Na prepared by embodiment 12Fe2(SO4)3The transmission electron microscope picture of@alumina composite materials;
【Fig. 3】It is Na prepared by embodiment 12Fe2(SO4)3The charging and discharging curve figure of@alumina composite materials.
Specific embodiment
Following embodiment is intended to be described in further details present invention;And the protection domain of the claims in the present invention It is not limited by the example.
Embodiment 1
The present embodiment comprises the following steps:
Step (1):The present embodiment design generation 0.03mol target products Na2Fe2(SO4)3@alumina composite materials, match somebody with somebody Solution 50mL processed, weighs the sodium sulphate of 0.03mol respectively, and the ferrous sulfate of 0.06mol is dissolved in the deionized water of 50mL, stirs Mix dissolving;
Step (2):It will be evaporated through the solution that step (1) is handled as stirring in 80 DEG C of oil baths to solution, obtained solid Powder is Na2Fe2(SO4)3Precursor product;
Step (3):By gained presoma solid product in hydrogen-argon-mixed (5%H2+ 95%Ar) atmosphere protection under, rise Temperature is to 350 DEG C, and for 24 hours, 5 DEG C/min of heating rate is to get to product Na for sintering2Fe2(SO4)3;
Step (3):By the Na obtained by step (3)2Fe2(SO4)3With 0.201g aluminium isopropoxides, acetone is used as grinding medium Matter, ratio of grinding media to material 10: 1, ball milling 6h, the powder dried is in hydrogen-argon-mixed (5%H2+ 95%Ar) in atmosphere, 250 DEG C are forged Burn 4h to get.
Button cell, material table are assembled into using sodium-ion battery composite positive pole manufactured in the present embodiment and sodium piece Chemical property seek peace as shown in the figure:
Fig. 1 shows to successfully synthesize Na2Fe2(SO4)3@alumina composite materials.
The Na of the visible synthesis of Fig. 22Fe2(SO4)3@alumina composite materials, particle diameter distribution is uniform, grain size 470nm, oxidation Aluminium coating thickness is 50nm.
Fig. 3 is Na2Fe2(SO4)3@alumina composite materials are assembled into button cell in lower initial charge specific capacity with sodium piece For 83mAh g-1, specific discharge capacity is 69mAh g-1。
Embodiment 2
The present embodiment comprises the following steps:
Step (1):The present embodiment design generation 0.03mol target products Na2Fe2(SO4)3@alumina composite materials, match somebody with somebody Solution 50mL processed, weighs the sodium sulphate of 0.03mol respectively, and the ferrous sulfate of 0.06mol is dissolved in the deionized water of 50mL, stirs Mix dissolving;
Step (2):It will be evaporated through the solution that step (1) is handled as stirring in 100 DEG C of oil baths to solution, obtained solid Powder is Na2Fe2(SO4)3Precursor product;
Step (3):By gained presoma solid product in hydrogen-argon-mixed (5%H2+ 95%Ar) atmosphere protection under, rise Temperature is to 350 DEG C, and for 24 hours, 5 DEG C/min of heating rate is to get to product Na for sintering2Fe2(SO4)3;
Step (4):By the Na obtained by step (3)2Fe2(SO4)3With 0.201g aluminium isopropoxides, acetone is used as grinding medium Matter, ratio of grinding media to material 10: 1, ball milling 6h, the powder dried is in hydrogen-argon-mixed (5%H2+ 95%Ar) in atmosphere, 350 DEG C are forged Burn 4h to get.
The battery assembling of the present embodiment resulting materials and test method are same as Example 1, Na2Fe2(SO4)3@aluminium oxide Composite material grain size is 350nm, and alumina-coated layer thickness is 50nm.Initial charge specific capacity is 76mAh g-1, discharge specific volume It measures as 69mAh g-1。
Embodiment 3
Step (1):The present embodiment design generation 0.03mol target products Na2Fe2(SO4)3@alumina composite materials, match somebody with somebody Solution 50mL processed, weighs the sodium sulphate of 0.03mol respectively, and the ferrous sulfate of 0.06mol is dissolved in the deionized water of 50mL, stirs Mix dissolving;
Step (2):It will be evaporated through the solution that step (1) is handled as stirring in 100 DEG C of oil baths to solution, obtained solid Powder is Na2Fe2(SO4)3Precursor product;
Step (3):By gained presoma solid product in hydrogen-argon-mixed (5%H2+ 95%Ar) atmosphere protection under, rise Temperature is to 350 DEG C, and for 24 hours, 5 DEG C/min of heating rate is to get to product Na for sintering2Fe2(SO4)3;
Step (4):By the Na obtained by step (3)2Fe2(SO4)3With 0.268g aluminium isopropoxides, acetone is used as grinding medium Matter, ratio of grinding media to material 10: 1, ball milling 6h, the powder dried is in hydrogen-argon-mixed (5%H2+ 95%Ar) in atmosphere, 250 DEG C are forged Burn 4h to get.
The battery assembling of the present embodiment resulting materials and test method are same as Example 1, Na2Fe2(SO4)3@aluminium oxide Composite material grain size is 350nm, and alumina-coated layer thickness is 70nm.Initial charge specific capacity is 72mAh g-1, discharge specific volume It measures as 60mAh g-1。
Comparative example 1
Step (1):This comparative example design generation 0.03mol target products Na2Fe2(SO4)3@alumina composite materials, match somebody with somebody Solution 50mL processed, weighs the sodium sulphate of 0.03mol respectively, and the ferrous sulfate of 0.06mol is dissolved in the deionized water of 50mL, stirs Mix dissolving;
Step (2):It will be evaporated through the solution that step (1) is handled as stirring in 140 DEG C of oil baths to solution, obtained solid Powder is Na2Fe2(SO4)3Precursor product;
Step (3):By gained presoma solid product in hydrogen-argon-mixed (5%H2+ 95%Ar) atmosphere protection under, rise Temperature is to 350 DEG C, and for 24 hours, 5 DEG C/min of heating rate is to get to product Na for sintering2Fe2(SO4)3;
Step (4):By the Na obtained by step (3)2Fe2(SO4)3With 0.201g aluminium isopropoxides, acetone is used as grinding medium Matter, ratio of grinding media to material 10: 1, ball milling 6h, the powder dried is in hydrogen-argon-mixed (5%H2+ 95%Ar) in atmosphere, 250 DEG C are forged Burn 4h to get.
The battery assembling of this comparative example resulting materials and test method are same as Example 1, Na2Fe2(SO4)3@aluminium oxide Composite material grain size is 1200nm, loses uniform alumina-coated layer.Initial charge specific capacity is 40mAh g-1, discharge specific volume It measures as 23mAh g-1。
Comparative example 2
Step (1):This comparative example design generation 0.03mol target products Na2Fe2(SO4)3@alumina composite materials, match somebody with somebody Solution 50mL processed, weighs the sodium sulphate of 0.03mol respectively, and the ferrous sulfate of 0.06mol is dissolved in the deionized water of 50mL, stirs Mix dissolving;
Step (2):It will be evaporated through the solution that step (1) is handled as stirring in 140 DEG C of oil baths to solution, obtained solid Powder is Na2Fe2(SO4)3Precursor product;
Step (3):By gained presoma solid product in hydrogen-argon-mixed (5%H2+ 95%Ar) atmosphere protection under, rise Temperature is to 350 DEG C, and for 24 hours, 5 DEG C/min of heating rate is to get to product Na for sintering2Fe2(SO4)3;
Step (4):By the Na obtained by step (3)2Fe2(SO4)3With 0.201g aluminium chloride, acetone is used as abrasive media, Ratio of grinding media to material is 10: 1, and ball milling 6h, the powder dried is in hydrogen-argon-mixed (5%H2+ 95%Ar) in atmosphere, 250 DEG C of calcinings 4h to get.
The battery assembling of this comparative example resulting materials and test method are same as Example 1, do not have aluminium oxide in product Clad, and a variety of dephasigns containing aluminium are formd, chemical property is very poor.Initial charge specific capacity is 20mAh g-1, discharge specific volume It measures as 8mAh g-1。