Effect of the particle size and the debinding process on the density of alumina ceramics fabricated by 3D printing based on stereolithography
Haidong Wu, Yanling Cheng, Wei Liu, Rongxuan He, Maopeng Zhou, Shanghua Wu, Xuan Song, Yong Chen
In this study, Al2O3 ceramics were printed by stereolithography from particles with different particle size distributions, which are the micro-sized Al2O3, nano-sized Al2O3, and a mixture of both. The influence of the particle size and the debinding method on the density and morphology of the sintered bodies were investigated. The density of the samples containing both micro-sized and nano-sized alumina particles is highest among the three samples. Furthermore, the samples subjected to the vacuum debinding showed a higher density compared with the samples subjected to the traditional thermal debinding. The results suggest that the combination of a powder with a bimodal particle size distribution and the vacuum debinding process offers an effective way to print 3D ceramics with a good performance through stereolithography.
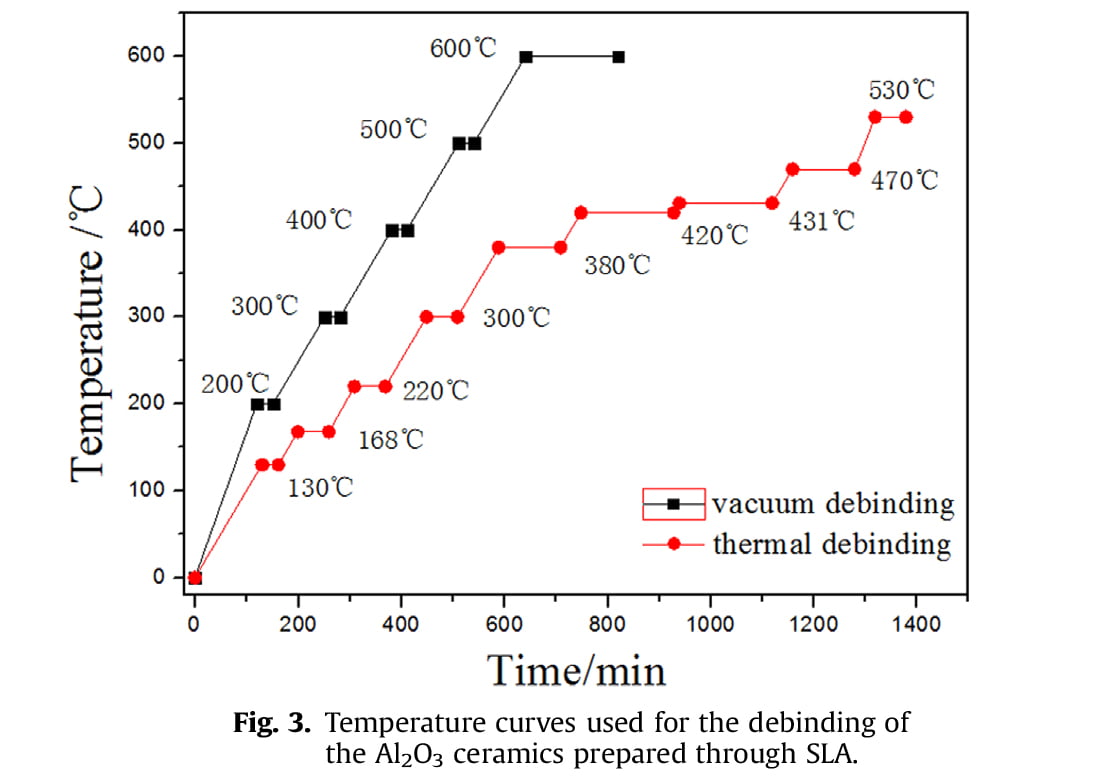
1. Introduction
3D printing is a layer-by-layer fabrication technique allowing to directly produce three-dimensional objects from a digital model. Stereolithography (SLA) is a 3D printing technique based on curing a photo-reactive resin with a UV laser or another similar power source, and is known for its high accuracy and excellent surface finishing [1–6]. Ceramic parts with complex 3D shapes can be manufactured using this method by mixing the ceramic powder and the UV-curable resin together analogously to the colloidal processing of ceramic powders. However, the mechanical and functional properties of the thus fabricated ceramics are not ideal due to the limited solids content of the ceramic powders [7,8]. As known, in colloidal processing, a low solid content usually results in a low density of the produced ceramics. Therefore, the sinterability and formability of ceramics prepared by SLA are inversely correlated.
When fabricating ceramic parts by SLA, the curing depth Cd is a crucial parameter which determines the accuracy of the formability. It is given by:
where d is the mean particle size of the ceramic powder, ϕ is the volume fraction of the ceramic powder in the suspension, λ is the wavelength of the irradiation, no is the refractive index of the resin, Δn is the difference in refractive index between the ceramic powder and the monomer solution, E is the exposure to provide polymerization of the monomer, and Ec is the critical exposure to provide polymerization of the monomer [9–11]. Compared with polymer-based SLA, additional factors related to the use of ceramics obviously affect the line width and the curing depth. Moreover, the traditional SLA equipment relies on the dispersions having viscosities lower than 5 Pa s (301/s) [12]. Thus, the particle size and the volume fraction of the ceramics must be adjusted to meet the requirements of both of the formability and sinterability. Meanwhile, a fine particle size and a high volume fraction are necessary to obtain ceramics with a high density.
Previous theoretical and experimental studies have demonstrated that an appropriate size distribution of the particles in the suspension promotes a dense packing of the particles in the cast body and, hence, increases the apparent density of the green body. In particular, Subbanna et al. [13], and Tari et al. [14] have shown that, in colloidal processing, it is possible to obtain high-density bodies using a bimodal particle size distribution in which fine and coarse powders are combined at an appropriate ratio. For instance,Zhou et al. [15] obtained a high concentrated aqueous ceramic suspensions by using a ceramic powder with a wide particle-size distribution. Fattahi et al. [16] reported that, compared with fibers, the reinforcing effect of Al2O3 platelets is due to two-dimensional stiffening. Olhero et al. [17] reported that the presence of coarse particles in the suspensions resulted in a shear-thinning behavior, whereas the compaction efficiency increased with the width of the particle size distribution [18]. Thus it is believed that controlling the particle size distribution, especially by adding coarser particles, may be an effective way to meet the requirements of the suspensions and the SLA process.
Furthermore, selecting an optimal sintering path guarantees a high density of the green body. So far, most studies focused on the formability during the SLA process, rarely considering the post-treatment process. However, the debinding is an important step of each slurry-based forming method. The residual carbides resulting from undecomposed organics are detrimental to the performance of the prepared ceramic bodies. Compared with the widely used thermal debinding process, a vacuum debinding process combines the debinding and the sintering cycle into a single processing step and allows to minimizes damage caused by the handling of the fragile debond parts [19].
In this study, Al2O3 ceramic parts were printed by stereolithography from particles with different particle size distributions, which are micro-sized Al2O3, nano-sized Al2O3, and a mixture of both. The influence of the particle size and the debinding method on the density and morphology of the sintered bodies were investigated. The density of the samples containing both micro-sized alumina and nanoparticles was the highest among the three samples. Furthermore, the samples subjected to the vacuum debinding showed a higher density compared with the samples subjected to the traditional thermal debinding. The results suggest that the combination of a powder with a bimodal particle size distribution and the vacuum debinding process offers an effective way to print 3D ceramics with a good performance through stereolithography.
2. Material and methods
2.1. Powder mixture preparation
A micro-sized Al2O3 powder and nano-sized Al2O3 powder with a particle size of 9mm and 50nm, respectively, were used as the starting materials in this study. Three types of samples were printed by digital micro mirror-assisted SLA from micro-sized Al2O3 powder, nano-sized Al2O3 powder, and a mixture of both at a 1:1 wt ratio. The starting materials used for the fabrication of each type of samples are listed in Table 1. The Al2O3 solids content for each sample was 65wt%. The mixture was then diluted in ethanol with ultrasound. After that, the mixture was ball-milled in a planetary ball mill for 6h using zirconia balls. The suspension was then dried in an oven at 60°C for 12h. Finally, the dried powder was sieved through a 100 mesh screen.
2.2. Preparation of the ceramic suspension
The premixed solution used to prepare the ceramic suspension consisted of four components: acrylamide (23.75wt%), N, N′ methylenebisacrylamide (1.25wt%), glycerine (10wt%), and deionized water (65wt%). The as-prepared powder was added to the premixed solution, and polyvinyl pyrrolidone (PVP) K-15 was used as the dispersant to form the ceramic suspension. The ceramic suspension was then ball-milled for 12 h using zirconia balls. The suspension was then de-gased for 30min using a vacuum mixer. In order to produce a UV-curable ceramic suspension, 2-hydroxy-2-methyl-1-phenyl-1-acetone was added to the ceramic suspension as initiator under ultrasound. In this study, the mass fraction of the photoinitiator was selected to 1wt% of the premixed solution.
2.3. Fabrication of the ceramic parts through stereolithography
The 3D model was created using the UG software, and then the Magics software was employed to generate the supporting structure and to slice the parts. The final data was then imported into the stereolithography machine. The alumina green body was obtained by stereolithography using the ceramic suspension mentioned above. A schematic illustration of the stereolithography process is shown in our previous literature [6,20,21].
Each individual pattern layer was cured by the ultraviolet laser selective scanning on the ceramic suspension. After the first layer was cured, the supporting platform was moved down, and the ceramic suspension was recoated on the cured surface with a blade. Then, the second layer was cured analogously. These steps were repeated until the whole green body of the alumina part was eventually obtained.
2.4. Post processing of the alumina green body
1) Drying
After the green body was obtained, the residual water in the sample had to be removed by drying. A novel drying approach based on using PEG 400 as the liquid desiccant was adopted in this study [6]. For the PEG-based extraction process, the sample was immersed in PEG 400, which was expected to result in a uniform extraction rate in all directions.
2) Debinding
The vacuum debinding was carried out in a tube furnace under low vacuum conditions. For comparison, a thermal debinding process was also performed. The profiles of the vacuum and thermal debinding are confirmed in the Result and discussion section.
3) Sintering
Regarding the densification sintering, Sample 1 and 2 were sintered at 1750°C and Sample 3 with only the nanoparticles were sintered at 1600°C for 4h in a furnace (Thermconcept, HTK 16/18, Germany).
2.5. Sample characterization
The micro-structure was characterized by scanning electron microscopy (JEOL JSM 6500F, JEOL, Japan). The thermal decomposition behavior was assessed by thermogravimetric analysis (TGA) and differential scanning calorimetry (DSC; Netzsch Instruments, Germany) under air flow using a heating rate of 20K/min. The apparent densities were determined employing Archimedes’ displacement method.
3. Results and discussion
3.1. Morphology of the Al2O3 green bodies
A micro-sized alumina powder with a large particle size was added to the ceramic slurry to reduce its viscosity, which is beneficial for the forming process. The morphology of the as-printed ceramic green bodies is compared in Fig.1. Any inhomogeneity in the green bodies may result in an accumulation of stress during sintering. As shown in Fig.1(a) and 1(c), both the micro-sized and the nano-sized Al2O3 particles are homogeneously distributed throughout the polymer matrix. In Fig.1(b), the Al2O3 nanoparticles are revealed to be embedded between the micro-sized Al2O3 particles.
3.2. TGA-DSC analysis
For slurry-based forming methods, the thermal decomposition behavior of the green part can be a guidance to establish a suitable debinding schedule for the ceramics. Fig.2 shows the TGA-DSC curve for the Al2O3 green body. The same curve was obtained for all three types of samples.
Theoretically, the organics decompose between 500 and 700°C. The DSC curve depicted in Fig.2 features three exothermic peaks at 390.5, 439.5 and 524.0°C, with the peak observed at around 439°C being the most prominent. The corresponding weight loss is illustrated in the DTG curve, and the total weight loss was up to 48.2%. The highest loss in weight of 23.89% occurred at 431.6°C. Afterwards, the weight loss curve became more stable and no change was recorded at temperatures above 600°C. This indicates that the decomposition is complete before the temperature reaches 600°C. In order to completely remove the organic components, the debinding process should reflect every detail of the observed decomposition behavior. Delamination, the formation of micro-cracks and the occurrence of unevenly distributed holes are common defects for such layer-by-layer printing processes. Therefore, the heating rate and the dwelling time must be carefully adjusted to avoid the formation of defects during the debinding process.
3.3. Debinding and sintering of the Al2O3 parts
The vacuum debinding process was designed considering the TGA results. The heating rate was kept as low as 1°C/min. The temperature was kept constant for a certain period of time when the temperature had reached a value corresponding to one of the exothermic peaks, and the dwelling time was the same for each of those temperatures. A thermal debinding process with a much more precise temperature adjustment was also conducted for comparison. The temperature curves used for the debinding process are shown in Fig.3.
The cross-sectional morphology of the samples subjected to the vacuum debinding and the thermal debinding process are compared in Fig.4 and Fig.5, respectively. The obtained relative densities are compared in Fig.6. For both debinding methods, there was no obvious delamination, and no cracks formed. Fig.4 (a) reveals a loose morphology with micro-sized Al2O3 particles piling up irregularly. According to Fig.6, the relative density of this sample was only 65.7%. Thus it could be seen that densification is difficult for micro-sized particles because the sintering kinetics is low due to the small surface energy. In comparison, Sample 3 with the nano-sized Al2O3 particles showed a much larger surface energy than Sample 1 , which made the densification less difficult. After sintering at 1600°C (1750°C for sample 1 and 2), the relative density increased to 89.2% (Fig.6), much higher than the density of Sample 1. It is shown in Fig.4(c) that nano-sized Al2O3 grains distributed homogeneously in the sintered body, but there are still some obvious pores in the corresponding microstructure. Fig.4 (b) shows a typical bimodal particle distribution with a mixture of micro-sized and nano-sized Al2O3 particles. As shown in Fig.4(b), the spherical alumina nanoparticles take up the gaps between the micro-sized grains. Hence, the relative density of this sample was the highest among the three samples (91.2%). This phenomenon could be explained by the effect of particle size combination. It has been proven that usually optimization of the grain composition is an effective way for raising the volumn fraction of the ceramic suspension and beneficial for reducing the viscosity of the ceramic suspension, thus probably the density of the sintered body made from the combination powder would be higher than the monolic powder [22–24]. Regarding the 3 samples subjected to the thermal debinding, the microstructure of Sample 1 shows the same feature with the sample subjected to the vacuum debinding, and also the relative density is 65.2% almost same with the relative density of Sample 1 via vacuum debinding. There are more pores existed in the sintered body via thermal debinding for Sample 2 and 3 compared with Sample 2 and 3 via vacuum debinding. The respective relative density of Sample 2 and 3 via thermal debinding is 83.2% and 82.2% compared with 91.2% and 89.2% via vacuum debinding.
The results of this study show that the density of the samples containing both micro-sized alumina and nano-sized particles is the higher than the monolic micro-sized powder and the nano-sized powder. Moreover, replacing some of the nanoparticles with low-cost micro-sizd Al2O3 may be a feasible low-cost approach for an SLA-based fabrication of Al2O3 ceramics. Meanwhile, the vacuum debinding resulted in a much higher relative density compared with thermal debinding.
4. Conclusions
In this study, Al2O3 ceramics were printed by stereolithography from particles with different particle size distributions, which are the micro-sized Al2O3, nano-sized Al2O3, and a mixture of both. The influence of the particle size and the debinding method on the density and morphology of the sintered bodies were investigated. The density of the samples containing both micro-sized and nano-sized alumina particles is highest among the three samples. Furthermore, the samples subjected to the vacuum debinding showed a higher density compared with the samples subjected to the traditional thermal debinding. The results suggest that the combination of a powder with a bimodal particle size distribution and the vacuum debinding process offers an effective way to print 3D ceramics with a good performance through stereolithography.